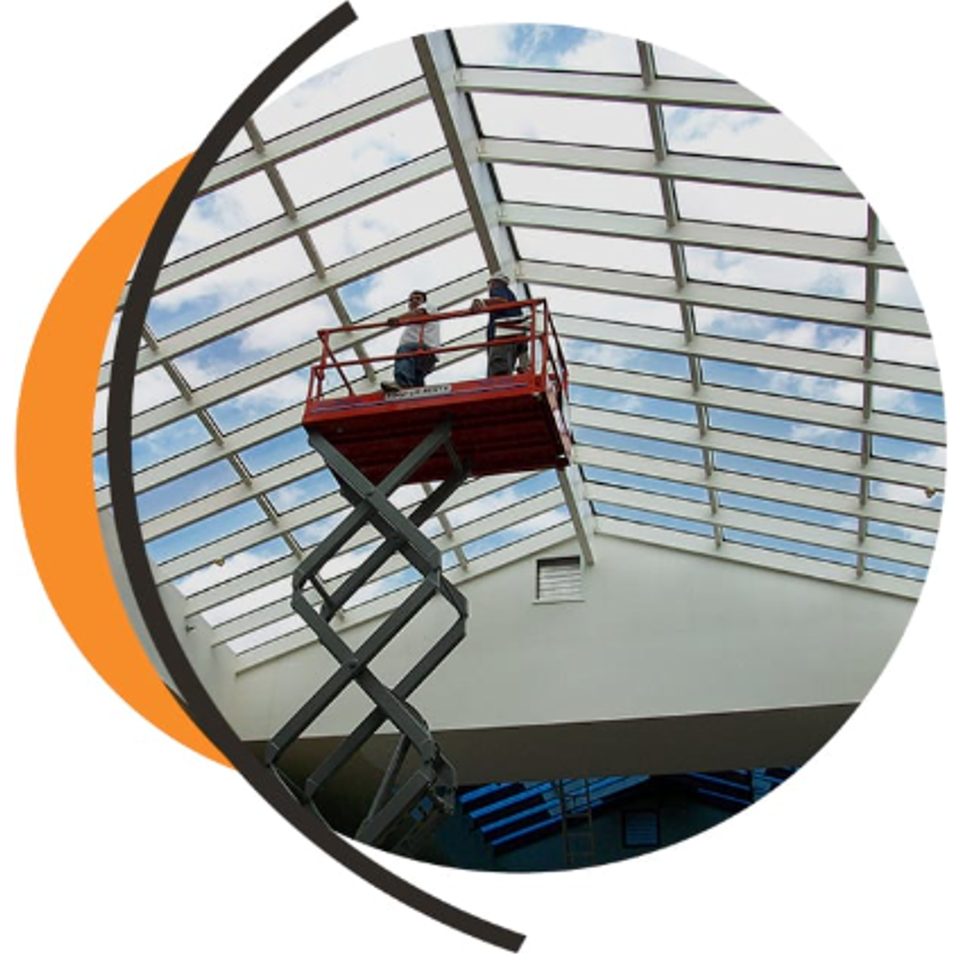
Safety
Accidents are preventable.
The bedrock of our safety is sobriety, ongoing training, a cooperative team, and careful planning of all construction activities. Your project should come to life as precisely as a Russian ballet. “How” is documented in our Equipment and Jobsite Safety Manual, Sub-Contractor Safety Manual, and the Project Specific Safety Manual we develop for your project.
Our culture of safety starts with Ownership, leading by example, and is cultivated by Project Managers, Site Superintendents, and a “one team” mindset.
The U.S. Department of Labor reports that drug and alcohol abuse causes 65% of on-the-job accidents*. Our Substance Abuse Policy includes testing: pre-placement, post-accident, for aberrant behavior, during routine medical procedures, for reasonable cause, and at random. A third-party administrator conducts this program in a strictly confidential manner.
Halcyon has earned and maintains a 0.85 MOD rate.
That is the lowest possible rate for a General Contractor. We have had 0 reportable injuries since incorporation of our company in 2012.
*SOURCE: https://ohsonline.com/Articles/2014/09/01/Drug-Testing-and-Safety
The bedrock of our safety is sobriety, ongoing training, a cooperative team, and careful planning of all construction activities. Your project should come to life as precisely as a Russian ballet. “How” is documented in our Equipment and Jobsite Safety Manual, Sub-Contractor Safety Manual, and the Project Specific Safety Manual we develop for your project.
Our culture of safety starts with Ownership, leading by example, and is cultivated by Project Managers, Site Superintendents, and a “one team” mindset.
The U.S. Department of Labor reports that drug and alcohol abuse causes 65% of on-the-job accidents*. Our Substance Abuse Policy includes testing: pre-placement, post-accident, for aberrant behavior, during routine medical procedures, for reasonable cause, and at random. A third-party administrator conducts this program in a strictly confidential manner.
Halcyon has earned and maintains a 0.85 MOD rate.
That is the lowest possible rate for a General Contractor. We have had 0 reportable injuries since incorporation of our company in 2012.
*SOURCE: https://ohsonline.com/Articles/2014/09/01/Drug-Testing-and-Safety